What is Condition Monitoring?
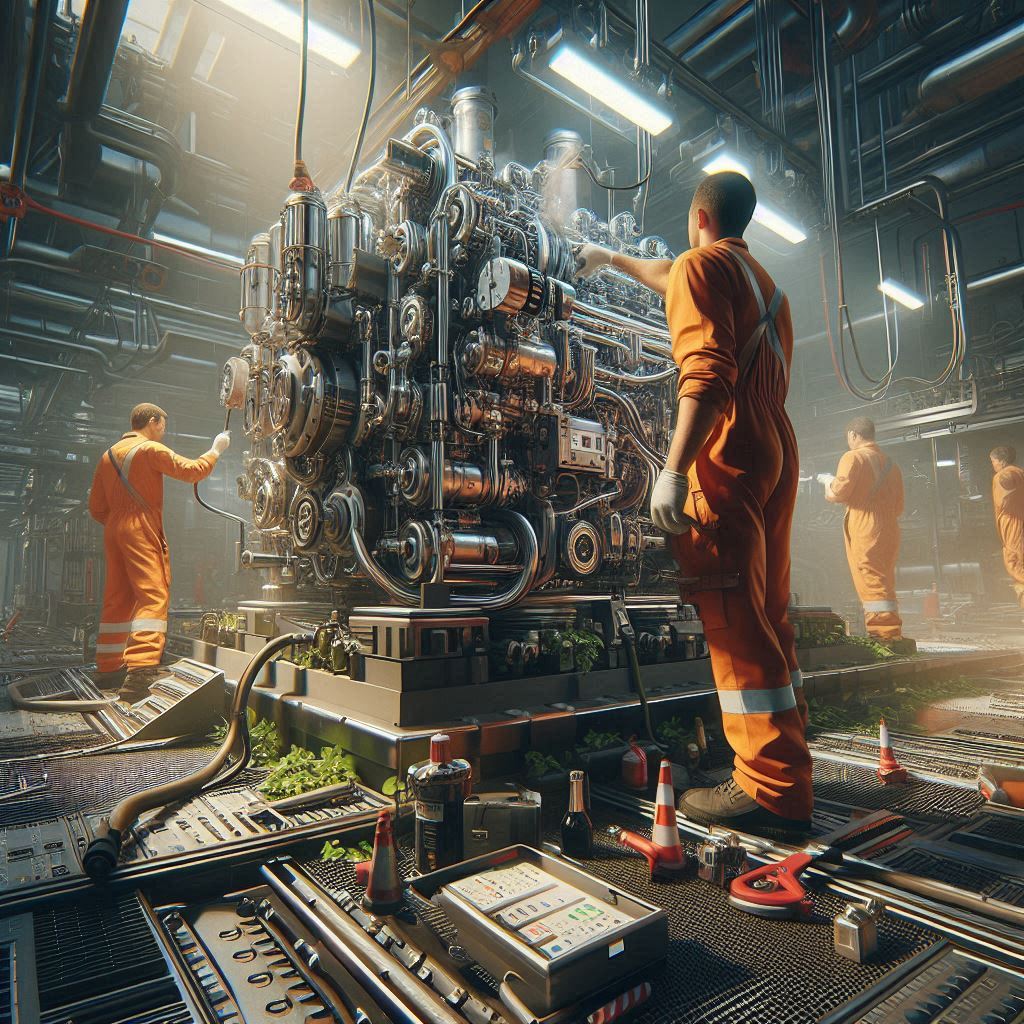
Condition monitoring is a proactive approach to maintaining the health and performance of machinery and equipment. By using various techniques and technologies to monitor the condition of assets, it aims to detect potential issues early, preventing unexpected failures and optimizing maintenance schedules. This approach not only enhances the reliability of machines but also contributes to cost savings and improved operational efficiency.
Understanding Condition Monitoring
The Importance of Condition Monitoring
Condition monitoring is crucial for any industry that relies on machinery and equipment. It helps in identifying faults and issues before they lead to severe failures, reducing downtime and maintenance costs. By continuously monitoring the condition of assets, companies can extend the lifespan of their equipment and improve overall performance.
The Basic Principle of Condition Monitoring
The basic principle of condition monitoring involves using sensors and data analysis tools to measure various parameters of machinery, such as vibration, temperature, and oil quality. By analyzing this data, maintenance teams can detect deviations from normal operating conditions, indicating potential problems that need to be addressed.
The Five Elements of Condition Monitoring
- Data Acquisition: Collecting data from sensors installed on the equipment.
- Data Processing: Converting raw data into a usable format.
- Condition Analysis: Analyzing the processed data to assess the equipment’s condition.
- Diagnosis: Identifying the specific issues or faults based on the analysis.
- Prognosis: Predicting future equipment conditions and remaining useful life.
The Four Pillars of Condition Monitoring
- Predictive Maintenance: Using data analysis to predict equipment failures and schedule maintenance accordingly.
- Preventive Maintenance: Regularly scheduled maintenance activities to prevent unexpected failures.
- Reliability-Centered Maintenance: Ensuring maintenance activities are aligned with the reliability and safety requirements of the equipment.
- Condition-Based Maintenance: Performing maintenance only when data indicates that it is necessary.
How Does Condition Monitoring Work?
Step 1: Install the Monitoring System
The first step involves installing a monitoring system, which includes sensors and data acquisition devices, on the machinery. These sensors measure various parameters such as vibration, temperature, and oil quality, providing real-time data on the equipment’s condition.
Step 2: Baseline Data Measurement
Once the monitoring system is installed, baseline data measurement is conducted to establish the normal operating conditions of the machinery. This baseline data serves as a reference point for identifying deviations and potential issues.
Step 3: Ongoing Monitoring
With the baseline established, the system continuously monitors the equipment, collecting and analyzing data in real time. Any deviations from the baseline are flagged for further investigation, allowing maintenance teams to address issues before they lead to significant problems.
Types of Condition Monitoring
Electrical Monitoring
Electrical monitoring involves measuring electrical parameters such as current and voltage to detect abnormalities that may indicate equipment issues.
Electromagnetic Measurement
This technique uses electromagnetic sensors to monitor the magnetic fields around machinery, helping to identify faults such as bearing wear or rotor imbalances.
Laser Interferometry
Laser interferometry measures the displacement and vibrations of machinery with high precision, providing detailed insights into equipment condition.
Motor Circuit Analysis
Motor circuit analysis evaluates the electrical health of motors, identifying issues such as insulation breakdown or winding faults.
Oil Analysis / Tribology
Oil analysis, or tribology, involves examining the properties of lubricants used in machinery. Changes in oil quality can indicate wear and tear, contamination, or other issues.
Performance Monitoring / Process Variable and Performance Trending / Observation and Surveillance
Performance monitoring tracks key process variables and trends over time, helping to identify deviations that may indicate equipment problems.
Radiography / Radiation Analysis / Neutron Radiography
These techniques use radiation to inspect the internal components of machinery, identifying faults such as cracks or material degradation.
Thermography / Temperature Measurements / Infrared Thermography
Thermography uses infrared cameras to measure the temperature of machinery components, identifying hot spots that may indicate overheating or other issues.
Ultrasonic Monitoring / Acoustic Analysis / Airborne Ultrasonic Monitoring
Ultrasonic monitoring detects high-frequency sound waves emitted by machinery, identifying issues such as leaks, cracks, or lubrication problems.
Vibration Analysis / Dynamic Monitoring
Vibration analysis measures the vibrations of machinery to detect imbalances, misalignments, or other mechanical issues.
Benefits of Condition Monitoring
Avoid Unplanned Downtime
By detecting issues early, condition monitoring helps avoid unplanned downtime, ensuring that machinery operates smoothly and efficiently.
Protect Your Other Assets
Condition monitoring helps prevent equipment failures that could damage other assets, protecting the overall health of the plant.
Eliminate Unnecessary Maintenance to Maximize ROI
By performing maintenance only when necessary, condition monitoring eliminates unnecessary maintenance activities, maximizing return on investment.
More Efficient Maintenance
Condition monitoring enables more efficient maintenance by providing detailed insights into the condition of machinery, allowing for targeted and effective maintenance actions.
Improved Safety
By identifying potential issues early, condition monitoring helps improve safety by preventing catastrophic equipment failures.
Improved Asset Efficiencies
Condition monitoring enhances asset efficiencies by ensuring that machinery operates at optimal performance levels, reducing energy consumption and operational costs.
Case Study: Grid Lifecycle Optimization with Enedis
In the case study of Enedis, the use of AI and software surveying for maintenance planning has proven to be highly beneficial. By leveraging AI for defect detection on their network, Enedis can anticipate renovation projects and allocate resources more efficiently. This proactive approach enables better maintenance planning, reducing costs and enhancing the overall reliability of the grid.
Disadvantages of Condition Monitoring
Installation Costs
The initial installation of condition monitoring systems can be expensive, including the cost of sensors, data acquisition devices, and software.
Operational Costs
Ongoing operational costs, such as data analysis and system maintenance, can add up over time.
Unpredictable Maintenance Scheduling
While condition monitoring aims to predict maintenance needs, it can sometimes lead to unpredictable scheduling if issues are detected unexpectedly.
Implementing Condition Monitoring
How to Get Started
Step One: Install the Hardware
Begin by installing the necessary hardware, including sensors and data acquisition devices, on the machinery to be monitored.
Step Two: Measure Your Data
Collect baseline data to establish normal operating conditions, providing a reference point for future monitoring.
Step Three: Monitor Your Machines
Continuously monitor the machinery, analyzing data in real time to detect deviations and potential issues.
Applications of Condition Monitoring
Online Condition Monitoring
Online condition monitoring involves real-time data collection and analysis, providing immediate insights into the health of machinery.
Wired vs. Wireless Condition Monitoring Systems
Wired systems offer reliable data transmission but can be more challenging to install and maintain. Wireless systems are easier to install and offer greater flexibility but may face issues with signal interference.
Latest Advancements in Condition Monitoring Technologies
Integration with IoT (Internet of Things)
The integration of IoT with condition monitoring systems allows for enhanced data collection and analysis, this solution provides deeper insights into equipment health.
AI and Machine Learning Applications
AI and machine learning are transforming condition monitoring by enabling more accurate predictions and automated data analysis.
Real-World Case Studies
Real-world case studies demonstrate the effectiveness of advanced condition monitoring technologies in improving equipment reliability and reducing maintenance costs.
Conclusion
Condition monitoring is an essential practice for maintaining the health and performance of machinery. By using advanced technologies and data analysis, industries can detect potential issues early, optimize maintenance schedules, and improve operational efficiency. Despite the initial costs, the long-term benefits of condition monitoring, such as reduced downtime and enhanced safety, make it a valuable investment.
FAQ
What are the 5 elements of condition monitoring?
The five elements of condition monitoring are data acquisition, data processing, condition analysis, diagnosis, and prognosis.
What are the four pillars of condition monitoring?
The four pillars of condition monitoring are predictive maintenance, preventive maintenance, reliability-centered maintenance, and condition-based maintenance.
What is the basic principle of condition monitoring?
The basic principle of condition monitoring involves using sensors and data analysis tools to measure and analyze various parameters of machinery, detecting deviations from normal operating conditions to identify potential issues.
How many types of condition monitoring are there?
There are several types of condition monitoring, including electrical monitoring, electromagnetic measurement, laser interferometry, motor circuit analysis, oil analysis, performance monitoring, radiography, thermography, ultrasonic monitoring, and vibration analysis.