How Eramet uses vision AI to enable its digital transformation
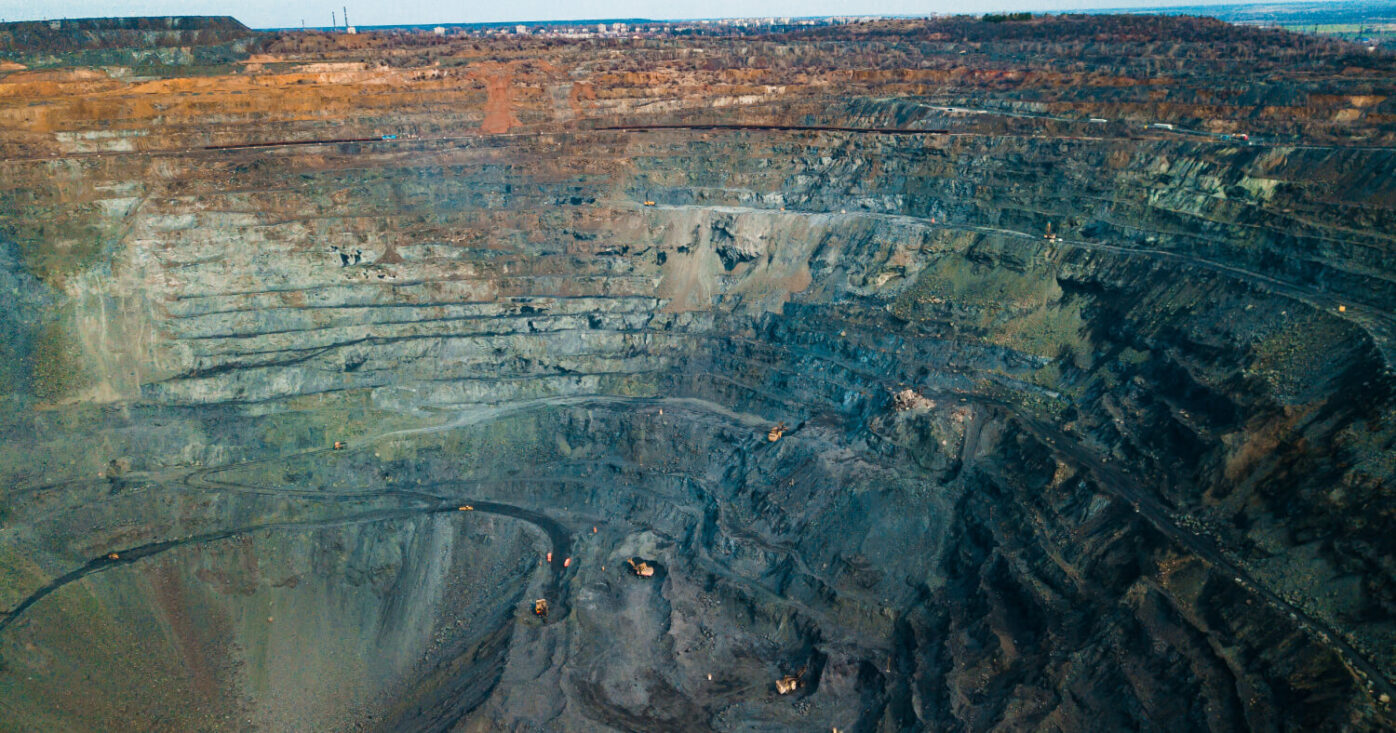
By leveraging visual AI, a global mining company achieves 30% reduction in the cost of tires for haul trucks, plus 15% reduction in fuel cost, and boosts productivity in the context of increased demand for nickel.
The Eramet Group, a top global mining and metals company based in France is committed to helping the world transition to clean energy sources. The company operates at about 50 sites across five continents. Mines operated by Eramet’s SLN subsidiary in New Caledonia are the world’s biggest ferronickel producers (used in stainless steel.) They’re also among the top 10 sources of nickel for other uses. Eramet’s executives see their company’s digital transformation as essential to enabling the change. This article shares how Eramet uses visual AI to reduce operating costs and increase production at one of the world’s most important nickel mines.
Context: Eramet embraces Mining 4.0 and visual AI to face the challenges of the industry
The demand for nickel is surging as the production of batteries is set for exponential growth. Eramet is a key global producer of nickel used in electric vehicles batteries, which can reduce dependence on fossil fuels.
According to the World Bank Group, clean energy needs will increase the demand for rare earth minerals by nearly 500% by 2050. Eramet has embraced Mining 4.0 and digital transformation as strategies to help them meet that demand. And the company is using visual artificial intelligence—or visual AI—as a cornerstone of its digital transformation.
World’s mines need a productivity boost to meet that demand
According to the Mining Productivity Index published by McKinsey & Company, on average, the world’s mines were operating at about 70% efficiency in 2017. This key mining metric, known as the MPI, had declined since the early 2000s and was primarily flat through 2013.
The MPI measures mine productivity across commodities. Its purpose is to assess industry drivers of productivity. It does so by tracking how much total material (ore and waste) mines move per unit of resource invested.
The main reason for the productivity drop, McKinsey said, was equipment breakdowns and stalled production. By reducing these causes, mines can increase productivity and throughput. McKinsey’s research uncovered these critical factors related to mine efficiency:
- Mining companies incur 30% to 50% of their operating cost on maintaining plants, fleet, and equipment.
- Urgent repairs and requests for corrective work cost mining companies 3 to 5 times more than the cost of planned maintenance.
Mines also need a profit boost
The profitability of the world’s top mines has also declined since its peak in 2006 (Figure 1).
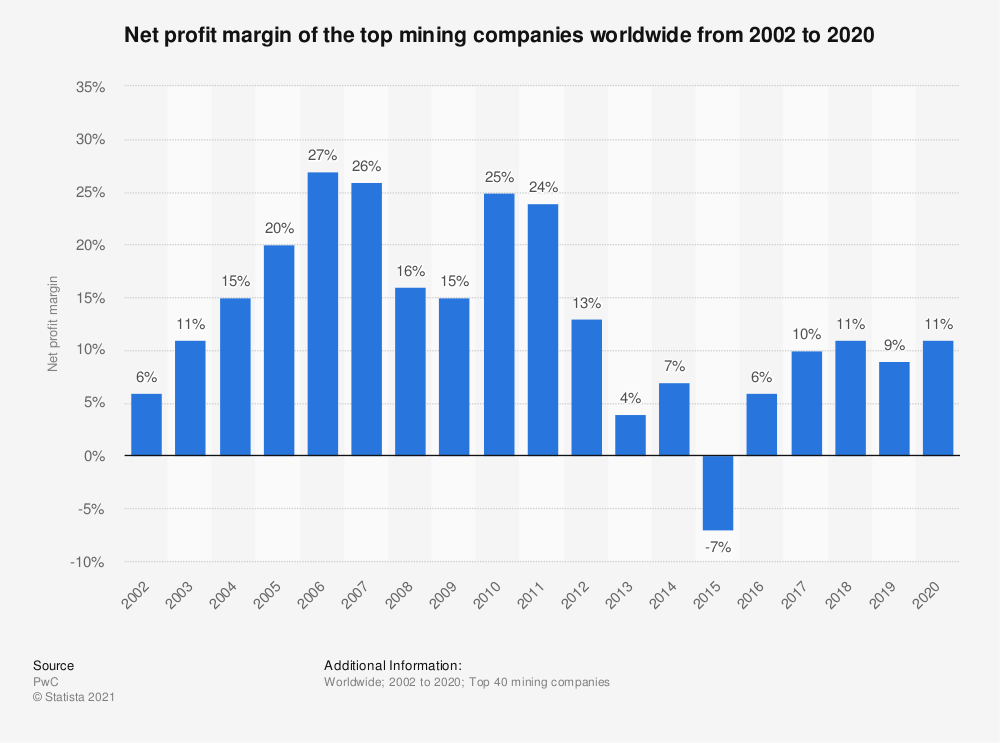
Figure 1. Profitability of the world’s major mines is less than half the level it was in 2006. Source: Statistica 2022
Mining 4.0 holds the promise of boosting production
Eramet has committed to the principles of Mining 4.0 in some of its operations. Mining 4.0 is a variant of Industry 4.0, a concept the German government introduced as part of its industrial strategy in 2011. The number four refers to the Fourth Industrial Revolution.
The primary goals of Mining 4.0 include:
- Speed production.
- Reduce downtime.
- Make operations more environmentally sustainable.
- Improve employee safety.
It achieves these goals through specific initiatives, including:
- The elimination of failures caused by humans.
- The minimization of the effects of all failures.
- The monitoring of the status and condition of the equipment.
- The reduction of maintenance costs.
Both Industry 4.0 and Mining 4.0 share design principles, including:
- Interconnection: Machines, devices, sensors, and people connect and communicate through the internet of things (IoT) or the internet of people (IoP).
- Transparency and communication: Operators have comprehensive information to make decisions.
- Technical assistance: Systems help humans make decisions and solve problems. They also help execute difficult or unsafe tasks.
- Decentralized decisions: Physical and cyber systems make decisions on their own and execute tasks with as little human intervention as possible.
A key element is to develop digital means to control physical assets. The enabling technologies are digitization, automation, analytics, artificial intelligence, and machine learning.
Remote operation centers serve as central control towers for mining companies
The concept of remote operation centers (ROCs) originated in the petroleum, defense, and aerospace industries. Their main goals were to:
- Keep people out of harm’s way.
- Optimize operations by making scarce expertise widely available across remote operations.
The concept is newer to the mining industry, where integrated remote operations centers (IROCs) serve as digital control towers. They provide strategic insights into all facets of operations.
Eramet began creating an IROC in 2017. Its goals are to:
- Improve operating performance.
- Achieve a competitive edge.
Eramet’s IROC monitors and controls global operations in real-time for the company’s 47 mines.
Alteia’s visual AI platform helps enable Eramet’s IROC
Eramet deployed Alteia’s visual AI platform as a critical element of their IROC.
The Alteia platform enables Eramet to create and maintain digital records of their sites. The data includes these elements and more:
- LiDAR point clouds generated by aerial drones
- Photographic images
- Geologic data from drilling
- Telematic data from equipment
- Photos and measurements from site surveys
The LiDAR point clouds serve as 3D maps known as digital twins. Eramet’s central operations team has fast and easy access to digital twins for all field sites. They can bring up the data simply by clicking a mouse.
Eramet’s SLN nickel mine in New Caledonia uses visual artificial intelligence to improve operating efficiency
Operators at SLN’s Tiébaghi site used visual AI to cut the cost of maintaining tires on haul trucks by 30%. They also reduced fuel consumption for haul trucks by 15%.
Here’s how they did it. The IROC at the Tiébaghi site receives real-time data from multiple digital sources, including photogrammetry and periodic LiDAR scans.
Digital scans create 3D digital twins of mine sites
From the 3D LiDAR scans, the software creates digital terrain models (DTMs) and digital surface maps (DSMs). A DTM (Figure 2) is a 3D digital representation of the “bare earth” physical terrain, including haul roads, highwalls, ponds, and more. It provides an X, Y, and Z coordinate for each point.
A DSM is also a 3D digital representation, but it also includes the reflective surfaces of buildings, equipment, safety blocks, and other elements that sit above the bare earth. Both kinds of maps can be accurate to within about a centimeter.
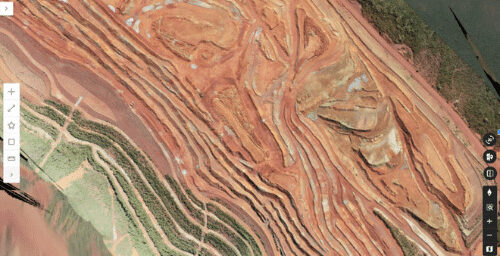
Figure 2. 3D digital terrain map. Software creates digital terrain models and digital surface maps of the mine. The data comes from 3D LiDAR scans executed by aerial drones.
Data from multiple sources highlights opportunities to improve
The IROC also receives time-series data about the condition of haul trucks, their location, and the behavior of their drivers. This data comes from telematic sensors in the trucks. The sensors send alerts about tire condition, the longevity of suspension systems, and the wear of trucks. Sensors also report engine speed, truck speed, fuel consumption, and other data.
From the truck data, SLN’s engineers could see that some engines were over-revving, and some drivers performed better than others. The challenge was to discover why some trucks needed more repairs than others. For that insight, engineers sought to link data from the trucks to data about the mine environment where the trucks operate.
Alteia helped SLN superimpose data from their haul trucks onto a 3D map of the haul roads. SLN could then see where in the mine the alerts occur. In addition, data from truck sensors enabled engineers to see engine speed, truck speed, and gear status of the haul trucks. Alteia then helped SLN create heat maps (Figure 3) showing where the stress on haul trucks was greatest.
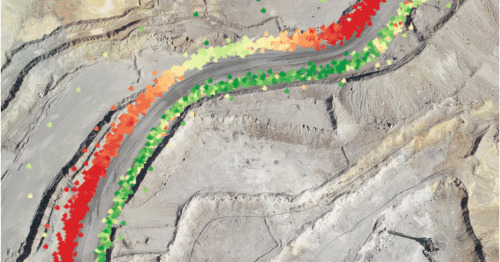
Figure 3. Heat map of where stress occurs on haul trucks. Software combines data from telematics and 3D models to map locations on haul roads where stress on trucks is greatest.
Next, Alteia helped add data about haul-road grades and surface conditions. Engineers could then spot uneven surfaces on the roads and correlate steep grades and fuel use (Figure 4). They could also see potholes, ruts, and rocks that stressed truck tires and structures.
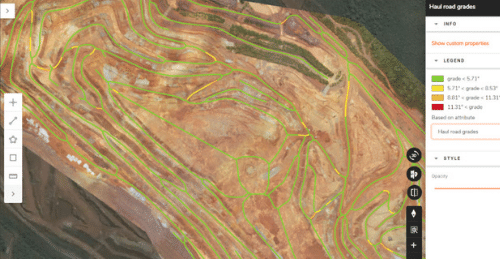
Figure 4. Map of haul road surface conditions. Software plots the geometry of haul roads by measuring grades and color-coding steep sections.
Finally, Alteia helped create a map that correlates alerts with the terrain of the mine and the condition and geometry of its roads (Figure 5). With this information, mine operators could level and repair roads, reduce steep slopes, and eliminate breaks in slopes.
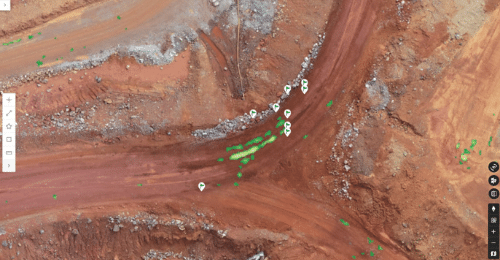
Figure 5. Haul-road sections that need work. Software superimposes telematic data from trucks. Sensors on the trucks send alerts when parts of the trucks are under stress. The map shows where road maintenance could reduce stress on trucks and cut maintenance costs.
Visual AI delivers added benefits
Besides reducing maintenance costs and fuel consumption, the mine also achieved these improvements:
- Improved safety of haul roads.
- Reduced survey cost and improved safety for topographers.
- 10x improvement on data processing and data availability.
Eramet can exchange data securely and efficiently across its operations, including with subcontractors. Alteia’s platform enabled Eramet to scale faster than it could by developing and running all its visual AI functions in-house.
Eramet has achieved the main goals for its IROC. However, the company continues to roll out additional capabilities and apply them across more mine sites.
Other major mining companies also use IROCs
Besides Eramet, other major mining companies have also deployed IROCs. They include:
- BHP Group (Melbourne) is the number 1 mining company globally.
- Anglo American (London), the number 5 globally.
- ArcelorMittal (Luxembourg City), the top steel manufacturer in North America, South America, and Europe. The vertically integrated company also operates mines.
In the most advanced implementations of IROCs, mining companies have round-the-clock, real-time visibility of their entire production chain, from “pit to port.”
For more on Mining 4.0 and the use of IROCs in the industry, please see the following helpful sources. For more about Alteia, visit www.alteia.com, and for more information like this, follow Alteia on LinkedIn.
Dig deeper
“Mining 4.0: How innovation is shaping mines of the future.” Benjamin Byrne. Chris Engdahl. May 5, 2021. Mining.com. [online article]
“McKinsey: Firms must invest in Remote Operating Centers.” Dominic Ellis. November 3, 2020. MiningGlobal. [online article]
“Remote operating centers in mining: Unlocking their full potential.” Roberto Gallardo. Dave Goddard. Stepan Görner. Bernardo Rubenstein. October 29, 2020. McKinsey & Company. [online article]
“Has global mining productivity reversed course?” Gauthier Canart. Lukasz Kowalik. Mukani Moyo. Raj Kumar Ray. McKinsey & Company. April 27, 2020. [online article]
“Behind the mining-productivity upswing: Technology-enabled transformation.” McKinsey & Company. September 25, 2018. [online article]
“Productivity across the global mining sector is starting to improve.” Nathan Flesher. Mukani Moyo. Stefan Rehbach. Eben van Niekerk. June 22, 2018. McKinsey & Company. [online article]