Operational Efficiency
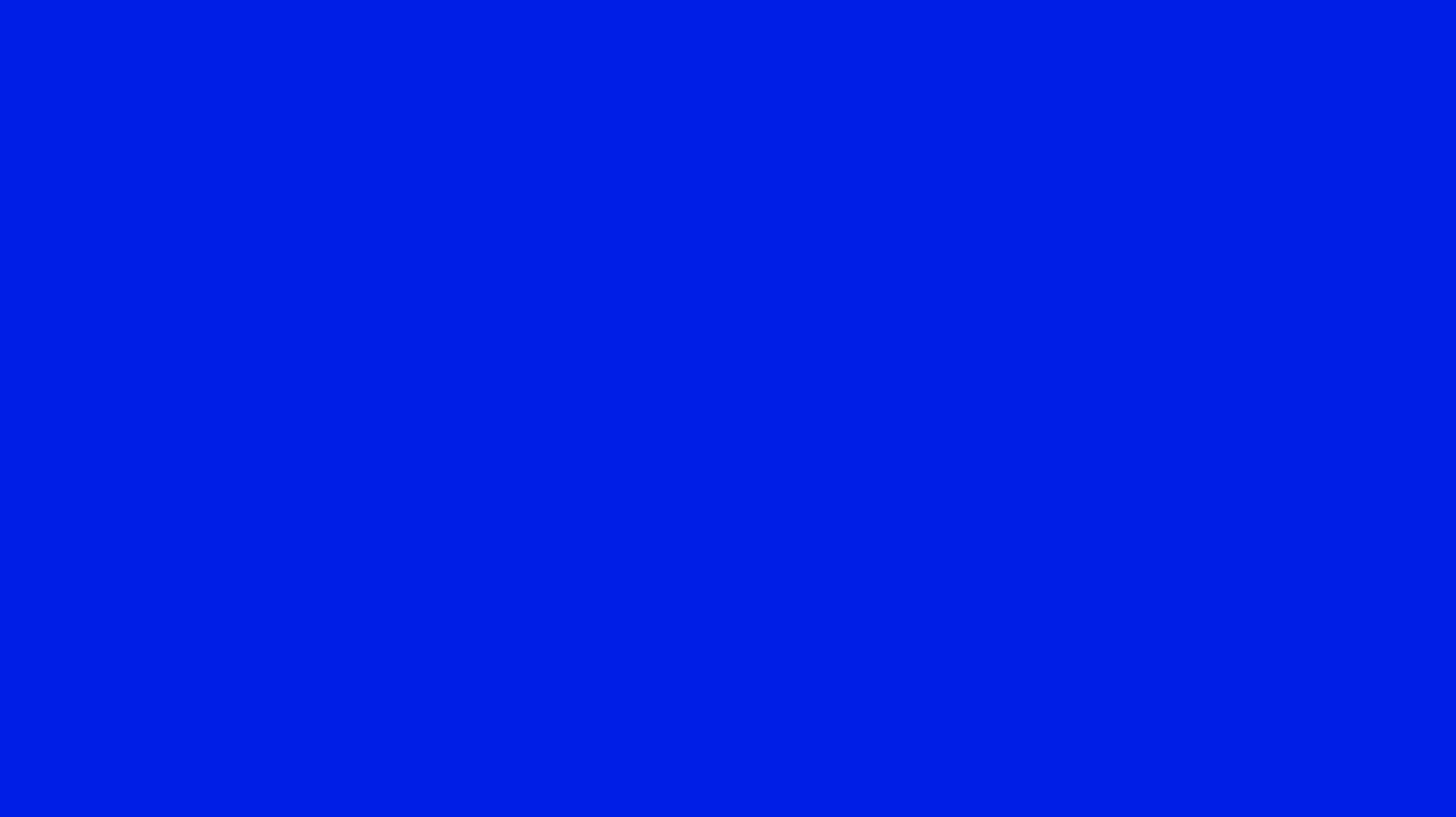
Understanding Operational Efficiency
Operational efficiency is crucial in today’s rapidly changing environment, where businesses must continuously adapt their strategies to meet evolving customer demands. It is essential for sustaining growth and profitability amidst constant disruptions. This section offers an overview of operational efficiency and its importance in today’s business landscape.
Definition and Importance of Operational Efficiency
Operational efficiency is the ability of a business to use its resources—time, labor, materials—effectively to produce the most output with the least input. This is essential as it leads to cost savings, better resource utilization, and a competitive edge. Efficient operations also enable businesses to respond faster to market changes and improve their overall profitability and sustainability.
Key Components of Operational Efficiency
Several elements contribute to achieving operational efficiency, including process streamlining, optimized resource allocation, and strong communication within the organization. A culture of continuous improvement is also critical, as it encourages innovation and adaptability. Together, these components enhance business performance, helping organizations meet market demands more swiftly and efficiently.
Productivity vs Efficiency: Where to Start?
Productivity measures the quantity of output, while efficiency assesses how well resources are used to generate that output. For example, increasing the number of units produced (productivity) doesn’t necessarily mean a company is using time or materials efficiently. Improving efficiency often yields quicker returns, as it directly reduces wasted resources—such as minimizing raw material waste in manufacturing or optimizing delivery routes in logistics. By focusing on efficient practices first, businesses can reduce costs and streamline operations, then work on increasing productivity, building a solid foundation for sustained growth.
Benefits of Improving Operational Efficiency
Improving operational efficiency offers numerous benefits. By focusing on efficiency instead of productivity, companies create a more agile and responsive organization capable of seizing new opportunities.
Here is a list of benefits of improving operational efficiency:
- Reduced Operational Costs: Streamlining processes helps cut down waste and resource usage, lowering overall costs.
- Faster Time-to-Market: Efficient operations allow businesses to deliver products and services more quickly, gaining a competitive edge.
- Increased Customer Satisfaction: Improved efficiency often leads to better service quality, faster response times, and enhanced customer experiences.
- Adaptability to Market Changes: An efficient organization can more easily adjust to evolving market conditions and customer demands.
- Agility and Responsiveness: Optimized internal processes create a more flexible organization, better positioned to seize new opportunities and drive innovation.
- Long-term Growth and Competitiveness: By continuously improving efficiency, businesses ensure sustainable growth and maintain their competitive advantage in the marketplace.
Strategies for Enhanced Operational Efficiency
To improve operational efficiency, businesses must adopt strategic approaches that streamline processes, eliminate waste, and leverage technology. Effective strategies focus on optimizing workflows, reducing inefficiencies, and integrating automation. This section explores various methods and tools that organizations can use to enhance their operational efficiency, ensuring long-term success and adaptability in a competitive marketplace.
Mapping and Optimizing Processes
Process mapping and optimization are essential to improve operational efficiency. Techniques such as value stream mapping, workflow analysis, and Lean Six Sigma help businesses identify bottlenecks and eliminate waste in their processes. These approaches provide a visual representation of workflows, making it easier to pinpoint inefficiencies and areas for improvement.
- Value Stream Mapping (VSM): This technique provides a visual representation of the entire production process, from raw materials to finished products. It highlights every step involved in delivering a product or service and helps businesses identify bottlenecks, delays, and non-value-added activities (waste). By mapping the value stream, companies can streamline operations, reduce lead times, and improve the flow of materials and information.
- Workflow Analysis: Workflow analysis involves examining the sequence of tasks and processes that make up a workflow. The goal is to understand how tasks are performed, how they are connected, and where inefficiencies (such as delays or unnecessary steps) may exist. This analysis helps identify opportunities for automating tasks, reallocating resources, or redesigning workflows to improve speed and efficiency.
- Lean Six Sigma: Lean Six Sigma is a methodology that combines the principles of Lean (focused on eliminating waste and improving flow) and Six Sigma (focused on reducing process variation and improving quality). It uses data-driven approaches to analyze processes, identify inefficiencies, and implement improvements. Lean Six Sigma helps companies streamline operations, enhance quality, and reduce costs by systematically addressing the root causes of inefficiency.
By using these techniques, businesses can gain a clearer understanding of their processes, eliminate inefficiencies, and improve both speed and quality, leading to better operational performance and cost savings.
Identifying and Eliminating Inefficiencies
To achieve operational excellence, businesses must proactively identify and eliminate inefficiencies. Strategies such as root cause analysis, performance audits, and employee feedback mechanisms can be used to uncover hidden inefficiencies in processes.
- Root Cause Analysis: This is a problem-solving method used to identify the underlying cause of issues or inefficiencies in a process. Instead of focusing on the immediate symptoms of a problem, root cause analysis digs deeper to find the source. By addressing these root causes, businesses can prevent the same problems from recurring, leading to more sustainable efficiency improvements.
- Performance Audits: Performance audits are evaluations of how well an organization’s processes, systems, or employees are functioning. These audits assess whether current operations meet performance standards and identify areas where improvements can be made. By conducting regular performance audits, businesses can continuously monitor their processes and ensure they are working as efficiently and effectively as possible.
- Employee Feedback Mechanisms: These are systems or methods (like surveys, suggestion boxes, or regular team meetings) that allow employees to provide input on process inefficiencies and suggest improvements. Employees often have first-hand knowledge of operational challenges, and their feedback can provide valuable insights into inefficiencies that might not be obvious at a higher level. Involving employees in continuous improvement fosters a collaborative culture where innovation and operational excellence thrive.
By addressing the root causes of problems, performing audits, and involving employees in continuous improvement initiatives, organizations can proactively eliminate inefficiencies, ensure continuous improvement, and cultivate a culture of operational excellence that promotes long-term growth and innovation.
Implementing Automation and Technology
Automation and technology play a pivotal role in enhancing operational efficiency. Enterprise resource planning (ERP) systems, robotic process automation (RPA), and artificial intelligence (AI) solutions streamline business operations by reducing manual tasks and minimizing errors. These technologies also accelerate decision-making processes, allowing organizations to respond quickly to market changes and operate more efficiently, ultimately gaining a competitive advantage.
Enhancing Efficiency with Surveying Software
Surveying software offers advanced tools, particularly in data aggregation and contextualization, that enhance operational efficiency through better data management, analysis, and reporting. These solutions allow businesses to visualize data more effectively, streamline reporting processes, and analyze operational performance in detail. By leveraging the capabilities of surveying software, organizations can make more informed decisions, optimize processes, and improve overall productivity.
Data Visualization for Better Decision-Making
Surveying software provides powerful data visualization tools that enable organizations to easily interpret complex data, transforming raw information into actionable insights. For example, a construction company using surveying software can visually track site progress through change maps that highlight areas where conditions have evolved, such as shifts in project timelines or resource allocation. Similarly, charts and graphs generated from customer feedback data can help retail businesses quickly spot trends in product performance or customer satisfaction, allowing them to adjust inventory or marketing strategies accordingly. These visual representations enable businesses to identify patterns and anomalies that may not be immediately evident in raw data, such as unexpected drops in productivity or sudden increases in equipment downtime.
This capability is crucial to enhance decision-making tools by presenting operational data in an intuitive, digestible format. By using visual insights, for instance, an energy company can track maintenance needs on pipelines via real-time dashboards, quickly responding to potential operational challenges before they escalate.
Ultimately, data visualization supports effective trend analysis, enabling businesses to make more informed strategic decisions and respond swiftly to evolving conditions, such as market shifts or operational bottlenecks.
Data Aggregation and Streamlined Reporting
Surveying software plays a critical role in data aggregation, bringing together information from various sources into one cohesive system. This consolidation eliminates manual data entry and enables streamlined reporting, which improves both efficiency and accuracy in data management. By offering centralized access to vital operational insights, businesses can make faster, more informed decisions. The ability to aggregate and report data efficiently directly contributes to greater operational efficiency across departments, supporting better overall performance and more cohesive organizational strategies.
Advanced Data Analysis for Operational Improvements
The advanced data analysis features in surveying software help businesses identify inefficiencies and opportunities for improvement. By leveraging detailed analytics, organizations can optimize processes and allocate resources more effectively. This is crucial for maintaining productivity, as it highlights areas for enhancement. The insights gained from data analysis are essential for driving continuous improvement and ensuring long-term operational success.
Measuring and Sustaining Operational Efficiency
Measuring and sustaining operational efficiency is crucial for long-term business success. By tracking performance through key metrics like Service effectiveness and Capacity utilization, and implementing continuous improvement practices, companies can maintain and enhance their efficiency over time. This section explores the essential tools and methodologies businesses can use to measure operational efficiency and sustain ongoing improvements for optimized Project performance and profitability.
Key Performance Indicators (KPIs) for Operational Efficiency
Key performance indicators (KPIs) are vital for measuring operational efficiency. Metrics such as cycle time, throughput, People resource utilization, and defect rates provide clear insights into the effectiveness of business processes. By regularly tracking these KPIs, organizations can identify inefficiencies, monitor progress, and make data-driven decisions to improve Financial performance. These metrics also highlight areas that require attention for continuous operational improvements, optimizing overall Investment returns.
Continuous Improvement Practices
Continuous improvement is essential for sustaining operational efficiency. Methodologies such as Kaizen, Total Quality Management (TQM), and Plan-Do-Check-Act (PDCA) cycles focus on fostering a culture of learning, adaptation, and innovation. By encouraging regular evaluation and Product optimization, these practices help organizations maintain high performance, adapt to changes in the market, and continuously improve their operations for long-term success, all while ensuring Margin improvements in efficiency.
Leveraging Survey Software to Measure and Sustain Operational Efficiency
Survey software provides essential tools for organizations to effectively measure operational efficiency and sustain long-term performance. Features such as automated data collection and real-time analytics enable businesses to monitor key performance indicators (KPIs) effortlessly, providing up-to-the-minute insights into their operational processes.
The software’s customizable reporting capabilities allow companies to tailor metrics, such as Goal alignment and Client satisfaction, to their specific needs, ensuring relevant data is easily accessible.
Additionally, survey software can bring uniformisation and standardization across a company with different sites.
Feedback loops and regular assessments supports continuous improvement and help businesses maintain efficiency over time. With real-time analytics, organizations can quickly identify areas requiring attention and make timely adjustments to optimize operations.
Case Study: TotalEnergies leverages Alteia’s AI platform to create a unified data framework
Alteia and TotalEnergies have partnered to consolidate visual data from sources like Lidar, drones, satellites, and ground equipment onto a single platform. This collaboration aims to create a “single source of truth” for enhanced decision-making, operational efficiency, and ESG (Environmental, Social, and Governance) compliance monitoring, particularly in reforestation efforts.
Alteia’s AI analysis of visual data from different sources enriched with other databases information (GIS, design files,…) provide real-time insights for proactive decision making, as well as enabling predictive maintenance for critical infrastructure such as solar farms.
Full case study here https://alteia.com/resources/blog/alteia-and-totalenergies-join-forces-to-unify-visual-data-for-unprecedented-insights/
Glossary
Kaizen
Kaizen is a Japanese term meaning “continuous improvement.” It refers to a business philosophy focused on constantly improving processes, products, and services through incremental changes. Kaizen involves all employees, from top management to front-line workers, and encourages small, consistent efforts to enhance efficiency and reduce waste, ultimately leading to better performance and productivity.
Total Quality Management (TQM)
Total Quality Management (TQM) is a management approach that seeks to improve the quality of all organizational processes, products, and services through continuous feedback and refinement. It emphasizes customer satisfaction, employee involvement, and process optimization. TQM integrates quality principles into every department and level of the organization to ensure that long-term success is achieved by meeting customer needs effectively and efficiently.
Plan-Do-Check-Act (PDCA)
The Plan-Do-Check-Act (PDCA) cycle, also known as the Deming Cycle, is a four-step management method used for continuous improvement and problem-solving.
- Plan: Identify the problem and devise a plan to improve or change a process.
- Do: Implement the plan on a small scale to test its effectiveness.
- Check: Monitor and evaluate the results of the test.
- Act: If successful, fully implement the plan; if not, revise and repeat the cycle. PDCA fosters iterative improvement and is a core part of many quality management practices.